Isolated Stackable DAQ Modules with Free Software
We offer a full line of low-cost Data Acquisition and Control modules which can be daisy chained together and connected to a single communications port of a PC or Laptop. Because these modules are stackable, allows the user to select any combination of features needed for their application, and to expand with additional features when necessary. Our Data Collection Software as pictured above is specifically designed to communicate with these DAQ modules and can be set up very quickly and easily by the novice using little or no programming skills. For more advanced programs with special requirements, our engineers can put together a custom software application for you. This can include the mapping of all of the data points to individual cells in your Excel Spreadsheet which will update automatically.
For Stand-Alone Operation without a PC, our Data Collection Software will run on any Single-Board Computer (SBC) that has the Windows operating system installed. This includes LattePanda, Udoo Bolt, UP Squared, Atomic Pi, Odroid H3+, Khadas Edge2, Hackboard 2, as well as many others. Once our software is installed on the SBC, even if a monitor, keyboard, and mouse are not needed in your final run-time application, all of the software logic that you program, such as Scripts, Conditionals, Data Logging, and DAQ Module Communications, can be utilized to its full extent. Furthermore, running the software application file from a USB flash drive, will allow easy transfer to and from a desktop computer for editing and/or access to the data log file without having to plug a monitor and keyboard into the SBC.
Analog Output Modules
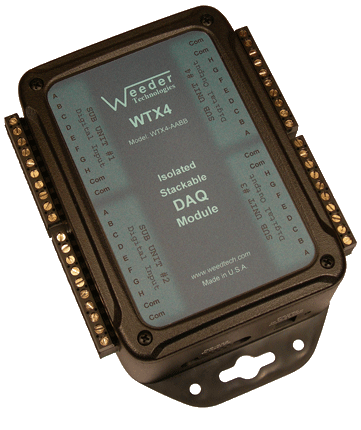 |
Isolated DAQ Module WTX4 Up to 16 analog output channels which can span from -10.00 to +10.00 VDC using 0.01 volt resolution. Built in S-Curve and Trapezoidal ramp generator with emergency stop switch input. Can also include a combination of other I/O types. read more... |
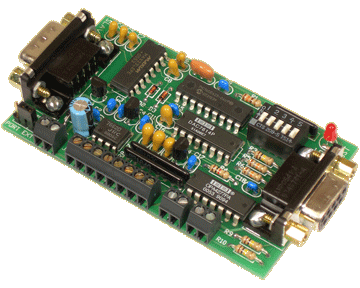 |
Analog Output Module WTDAC-M 4 analog output channels which can span from -10.00 to +10.00 VDC using 0.01 volt resolution. Built in S-Curve and Trapezoidal ramp generator with Pause switch input. read more... |
Analog Output Definition
Controlling machinery using a computer is a vital requirement of any industrial process or control operation. Many machines such as motor speed controllers, hydraulic presses, flow valves and actuators, accept a DC control signal to vary its output. However, a computer only has the ability to output binary digital numbers via the USB or RS232 port, not a variable DC voltage. An analog output circuit, or D to A converter (DAC), is needed to change the digital stream coming from a computer's output port to an analog voltage which can then be used to control the machinery. The Analog Output modules shown here have all the necessary D/A circuitry for this conversion including many advanced features not seen in most DAQ products on the market.
Stackable Capability
Stackable refers to the ability to connect multiple units together and share a single communications port of a host PC, laptop, or Single Board Computer (SBC). The DAQ modules are offered in two different footprints as shown above, enclosed in a case with full electrical isolation, or a non-isolated bare OEM circuit board. Both of these versions are stackable and can be mixed together if desired. The communications bus uses a stratagem based on the Carrier Sense Multiple Access (CSMA/CD) protocol. Carrier Sense (CS) is the monitoring of the data bus for a period of inactivity before a DAQ module is allowed to begin its own transmission. Multiple Access (MA) means that once the bus is free, every DAQ module in the network has an equal opportunity to transmit a frame. And Collision Detection (CD) uses non destructive bit wise arbitration to preserve the integrity of a data frame when two or more DAQ modules try to transmit at the exact same time. And since the data frame that wins arbitration remains intact during a collision, there is no additional communications delay when a collision occurs no matter how often it happens.
Host Communications
To communicate with the DAQ modules, commands are sent to the individual units by including a header character at the beginning (the address) so that it can be routed to the appropriate unit. If using multiple units connected together, the DIP switch for each unit should be set to a different position so that it will be assigned a different header character. Each DAQ module has its own command set used to configure it, operate the functions, and to read data from it. These commands are listed in the product data sheets. A typical command string looks like this:
HCNV{cr}
H = Header Character
C = Command Character
N = Channel Number (if applicable)
V = Value (if applicable)
{cr} = Carriage Return
If using our ModCom HMI software, the carriage return is not necessary because ModCom automatically inserts this at the end of each command string. ModCom has a communications dialog box which can be used to transmit individual commands to the DAQ modules and see the data coming back. This is helpful in learning the style of the command-set protocol and testing the hardware that's attached to the DAQ module. It is highly recommended that this testing be done prior to setting up any complex control programs.
Voltage Output & Ramping
Each output channel of the Analog Output DAQ units emit a control voltage which is dictated by the host that can be used to control equipment or machinery that accepts a ±10V control signal. A built-in ramp generator is included that can use a trapezoidal shaped slope profile or an S-curve shaped slope profile and allows the host to initiate a ramping function for a machine which will execute autonomously without guidance from the host. Once the output signal reaches the target voltage, the ramping will terminate automatically. This is very useful if the ramp rate is too fast for the host to keep up using individual voltage set points, or if the host needs to send commands to other DAQ units while the ramp is executing.
Note, these outputs do not deliver enough current to directly drive a load. If wishing to control the current driven thru a load, use the PWM output of a Digital Output unit instead which can deliver up to one full amp.
Copyright © 1998-2025 by Weeder Technologies. Made in USA.
|