Load Cell Interface Modules
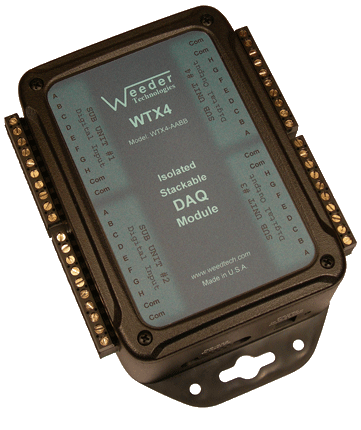 |
Isolated DAQ Module WTX4 Hooks up to load cells and measures force or weight. Up to 16 input channels with 20-bit A/D resolution. Easy 2-point calibration to set zero and full scale readings. Can also include a combination of other I/O types. read more... |
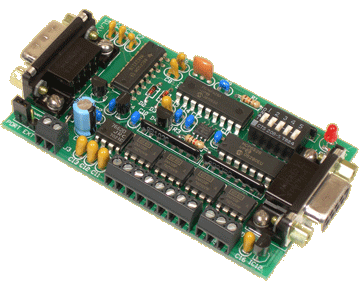 |
Analog Input Card WTAIN-M Hooks up to load cells and measures force or weight. 4 input channels with 20-bit A/D resolution. Easy 2-point calibration to set zero and full scale readings. read more... |
Load Cell Interface Definition
A typical load cell is used to measure weight, force, pressure, or tension, and is commonly used in an industrial setting for various functions. For example, it can be used on a production line to determine the quantity of product pieces being added to a container, or used in a testing application to determine the amount of force a product can withstand before failure. These load cells use a wheatstone bridge to convert the pressure to a voltage which can be measured by a load cell interface module such as what's shown above. These modules read the voltage and convert it to a digital format which can be delivered to a host computer via the USB or RS232 port. These modules can also be calibrated by the user to convert the readings to any engineering units of choice so that the number shown on the computer screen directly represents the information of interest.
Stackable Capability
Stackable refers to the ability to connect multiple units together and share a single communications port of a host PC, laptop, or Single Board Computer (SBC). The DAQ modules are offered in two different footprints as shown above, enclosed in a case with full electrical isolation, or a
non-isolated bare OEM circuit board. Both of these versions are stackable and can be mixed together if desired. The communications bus uses a stratagem based on the Carrier Sense Multiple Access (CSMA/CD) protocol. Carrier Sense (CS) is the monitoring of the data bus for a period of inactivity before a DAQ module is allowed to begin its own transmission. Multiple Access (MA) means that once the bus is free, every DAQ module in the network has an equal opportunity to transmit a frame. And Collision Detection (CD) uses non destructive bit wise arbitration to preserve the integrity of a data frame when two or more DAQ modules try to transmit at the exact same time. And since the data frame that wins arbitration remains intact during a collision, there is no additional communications delay when a collision occurs no matter how often it happens.
Host Communications
To communicate with the DAQ modules, commands are sent to the individual units by including a header character at the beginning (the address) so that it can be routed to the appropriate unit. If using multiple units connected together, the DIP switch for each unit should be set to a different position so that it will be assigned a different header character. Each DAQ module has its own command set used to configure it, operate the functions, and to read data from it. These commands are listed in the product data sheets. A typical command string looks like this:
HCNV{cr}
H = Header Character
C = Command Character
N = Channel Number (if applicable)
V = Value (if applicable)
{cr} = Carriage Return
If using our ModCom HMI software, the carriage return is not necessary because ModCom automatically inserts this at the end of each command string. ModCom has a communications dialog box which can be used to transmit individual commands to the DAQ modules and see the data coming back. This is helpful in learning the style of the command-set protocol and testing the hardware that's attached to the DAQ module. It is highly recommended that this testing be done prior to setting up any complex control programs.
Calibration Mode & Range
Each of the load cell input channels of the DAQ modules shown above can be set up to use 1 of 5 different calibration modes and input voltage ranges. For each input channel there are three factory calibrated modes which will return the results listed in voltage, and two user programmable custom modes which will return the results listed in any direct linear engineering units of choice. To calibrate a custom mode, first set the zero point, then either apply a known stimulus and tell the module what number you want to see on the computer screen, or tell the module what exact voltage you want to represent one unit of measurement. The gain and offset for this particular input channel will be automatically
re-calibrated to meet this criteria. For more information, see "User Programmable Modes" shown below.
Input Channel Scanning
During normal operation, the Load Cell Interface module continuously scans all channels in the background regardless of whether or not they are being polled by the host. The full
20-bit A/D results of each channel is stored in its own circular buffer which will always hold the most recent 8 samples. At any time a READ command is issued, the 8 samples associated with that particular channel are average together and the results will be the data which is returned to the host. This 8 times averaging smoothes out the readings and reduces the jitter shown on the computer screen.
User Programmable Modes
The Load Cell Interface modules incorporate a
32-bit floating point math routine which provides data conversions using calibration coefficients stored in non volatile memory. Each of the modes selected with the MODE command has its own set of calibration coefficients. There are two modes which can be programmed by the user to display the results of each READ command in the linear engineering units preferred. The span of the A/D converter is extended across the range of each mode and determines the maximum resolution available. Mode 4 has a range of -8V to +10V and a resolution of 22µV. Mode 5 has a range of -0.6V to +0.6V and a resolution of 1.4µV. Each mode can be individually programmed using one of two methods, SPAN or FACTOR.
SPAN can be used if a known output reading can be generated by the load cell. Sensor manufacturers often include a shunt resistor for this purpose and when attached to the sensor's bridge, will cause it to output a voltage which represents a specific reading. Applying a known weight to a load cell also works well. After setting up the sensor so that it outputs the known reading, transmit the SPAN command with the value field containing the reading that should be displayed on the computer screen. Multiplying the value by multiples of 10 will increase the resolution. For example, if applying a 50-lbs weight to a load cell, transmitting a value of 5000 in the SPAN command will set up the channel to display its readings in 0.01 lbs increments. The DECIMAL command can then be used to set up the channel to automatically insert a decimal point in the correct position of each reading if desirable.
FACTOR can be used if the actual voltage that equals one unit of measurement can be determined. To calculate this voltage in mV, use the factory listed output of the load cell in the following equation:
value = Out * E / FS where:
Out = Output of the load cell in mV/V.
E = Excitation voltage applied to bridge.
FS = Full scale capacity of the load cell.
For best results, the excitation voltage should be measured directly at the bridge using the same load cell input channel and lead wires that will be attached to the bridge output itself. Transmit the FACTOR command with the value field containing the results of this equation. Dividing the value by multiples of 10 will increase the resolution displayed on the computer screen in the same way as multiplying the value used in the SPAN command, as discussed earlier.
Input Voltage Range
Each of the input channels of the Load Cell Interface module has a common mode range of ±10V regardless of the MODE it is set to or the magnitude of the differential voltage it is measuring. Both positive and negative inputs must remain inside this range at all times or conversion errors will result. If connecting to a bridge sensor such as a load cell, the excitation voltage applied to the load cell bridge must be less than 20V in order to keep the inputs within this common mode range. An excitation of 5V to 15V is recommended for proper operation.
Copyright © 1998-2024 by Weeder Technologies. Made in USA.